Alright, let’s talk about this coiling metal thing. I ain’t no fancy expert, ya hear? But I’ve seen things, done things, and I can tell ya a thing or two.
First off, what is this coiling metal all about? Well, it’s like takin’ a piece of metal, long and flat, and then you curl it up, you know? Like rollin’ up a rug, but with metal. They use it for all sorts of things, I hear. Wire, springs, parts for machines, you name it.
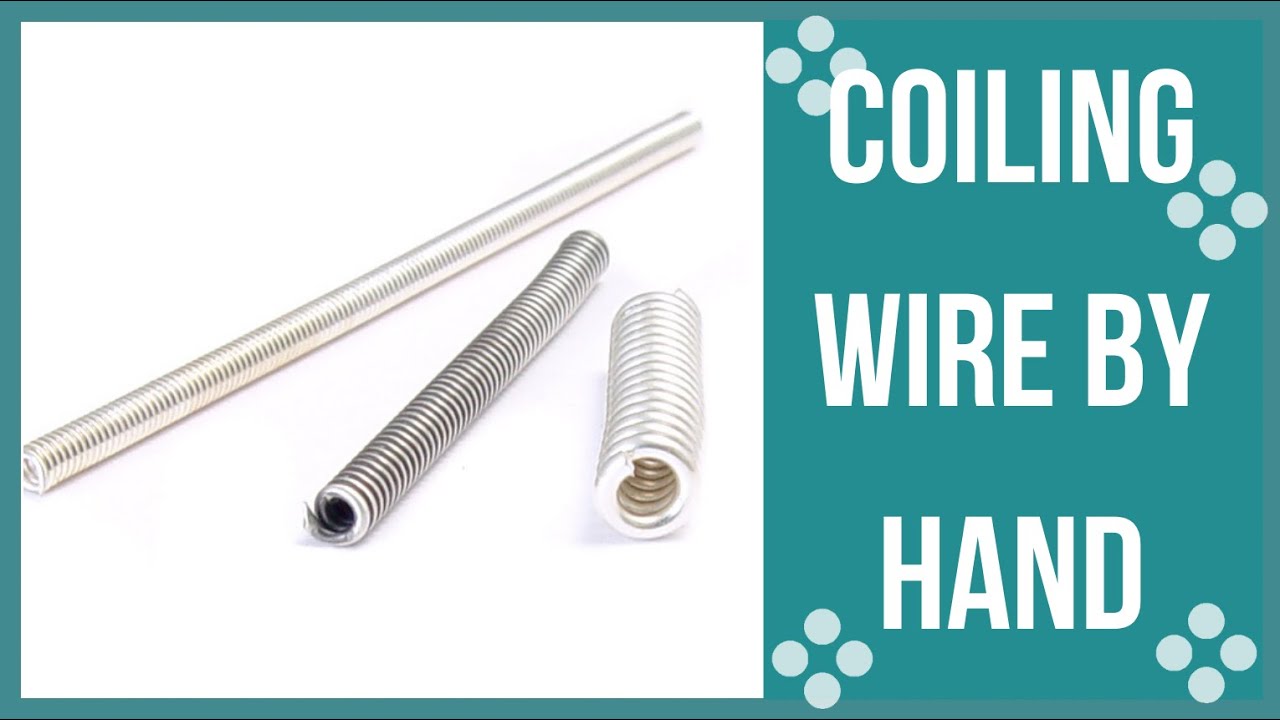
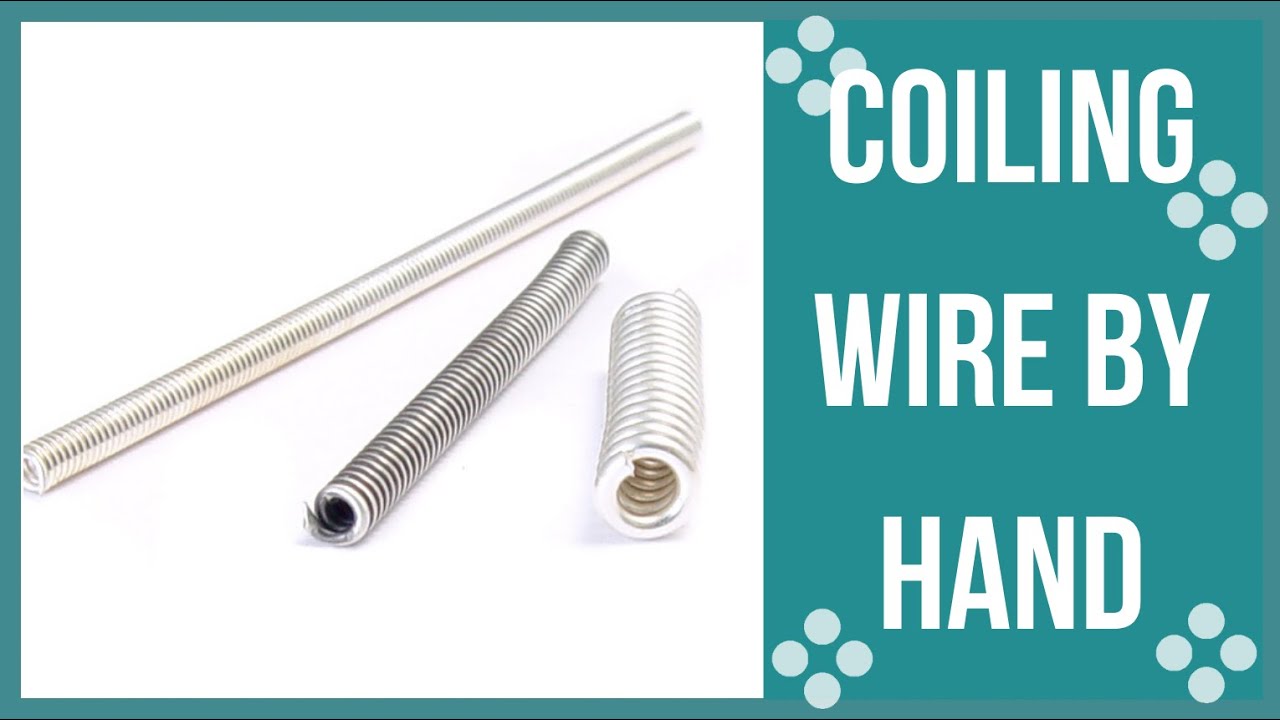
Now, how do you do it? That’s where it gets tricky. There’s machines, big ol’ things, that do the coiling. But before you even get to the machine, you gotta do some groundwork. You gotta pick the right metal, the right thickness, the right everything. It’s like bakin’ a cake. You can’t just throw anything in there and expect it to come out right.
- First, you gotta get your stuff ready. That means the metal, the tools, whatever you need.
- Then, you gotta set up that coiling machine. Make sure it’s all greased up and ready to go.
- Next, you feed the metal into the machine, nice and slow.
- Then, you fire that thing up and let it do its work. It’ll start curling that metal up, just like you want it.
But it ain’t always that simple. Sometimes things go wrong. The metal might kink up, or the machine might get stuck. You gotta keep an eye on things, make sure it’s all going smooth. And if it ain’t? Well, then you gotta figure out what’s wrong and fix it. That’s the hard part, I tell ya.
Troubleshooting, they call it. Sounds fancy, but it just means figuring out what went wrong and fixin’ it. Maybe the metal’s too thick, maybe the machine ain’t set right, maybe the moon’s in the wrong phase, who knows? You gotta try different things, see what works. It’s like tryin’ to get a mule to pull a plow. Sometimes it just won’t budge, and you gotta sweet talk it, or maybe give it a little kick in the behind.
Sometimes, after you coil the metal, you gotta heat it up. Heat treat, they say. That makes it stronger, tougher. It’s like bakin’ that cake again. You gotta get the temperature just right, or it’ll be a mess. Too hot, it’ll melt. Too cold, it’ll be brittle. It’s a real balancing act, I tell ya.
And then there’s testing. You gotta make sure them coils are good and strong, that they’ll hold up to whatever they’re supposed to do. You can’t just send out a bunch of flimsy coils and expect folks to be happy. They’ll come right back and complain, and then you’ll be in a whole heap of trouble.
Now, I’ve heard tell of this copper clad aluminum. They say it’s the new hot thing in coiling. Like a fancy new dress, everyone wants it. It’s lighter than copper, cheaper too, I reckon. But is it any good? That’s the question. I guess it depends on what you’re usin’ it for. Some folks swear by it, some folks stick to the old ways. Me? I ain’t got no dog in that fight. I just use what works.


And speakin’ of different ways, there’s more than one way to coil metal. You can slit a big coil into smaller ones, you can cut it into shapes, you can do all sorts of things. It all depends on what you need. It’s like a quilt, you know? You can make it big, you can make it small, you can make it all sorts of patterns. It’s up to you.
So, that’s the long and short of it. Coiling metal ain’t rocket science, but it ain’t easy neither. It takes skill, it takes patience, and it takes a whole lotta common sense. But if you do it right, you can make some mighty fine things. Things that last, things that work, things that people need. And that’s somethin’ to be proud of, I reckon.
And remember, if you want to prevent your coil from coiling before you’re ready, you gotta handle it right and keep it in a good place, don’t just throw it around like it’s trash.
Mastering metal fabrication, that’s what they call it. But it’s more than just fancy words, it’s about knowin’ what you’re doin’ and doin’ it right. Plan it out, choose the right metal, use the right tools and that is the key I think.